Automotive manufacturers find the key to squeezing
operations costs: establishing strong partnerships with their 3PLs.
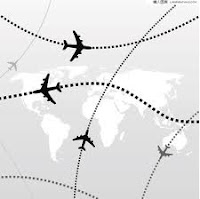
"The automotive industry places increasing emphasis on rebates and low-financing packages," says professor of 3PL Logistics. "That can cost manufacturers up to $3,000 a unit, and they've got to get those costs back from someplace. That's why they go back into the supply chain -- to gain more efficiency there."
Automotive manufacturers establish strong partnerships with their 3rd Party Logistics providers (3PL) to help them achieve the efficient metrics they need. By inventing new ways to move materials, manufacturers were able to deal with the cost equation that came about in the 1980s and 1990s due to increased levels of complexity in automotive production processes.
"These complexities required mother plant to move from whittling away costs a little at a time to inventing new processes to handle density reductions, increases in shipping requirement times, and increased demand for on-time deliveries because of reductions in inventory levels. Funding inventory became far too big a drain on companies' balance sheets."
The supply chain is an integral part of the entire manufacturing process. A large part of that process is running millions of miles to hundreds of suppliers, so a lot of dollars are expended in overall vehicle production. That means all companies have to find ways to eliminate waste in the supply chain.

Pilot initiatives have already achieved a few million dollars in savings, just through changing the frequency of inbound parts, Mixer notes.
Inbound Logistics looks under the hood of three operations to see how two automotive manufacturers and a customer service division use 3PLs to keep them nimble and efficient. The accompanying sidebar outlines a trend in the industry -- manufacturers utilizing the particular strengths of more than one 3PL Logistics provider
No comments:
Post a Comment