One method of improving surface of the material can be implemented by coating the suitable substance in from of coating layer or thin film having high quality. It can categorize into 2 large groups:
1. Chemical Vapor Deposition (CVD) and 2. Physical Vapor Deposition (PVD). Each method is suitable for each type of work. Currently, the vacuum deposition of PVD is getting the interest from the industrial sector in the country very much. The method of deposition by sputtering (one technique of PVD) in particular has been conducted R&D in every aspect from the equipment concerned, technique of coating layer’s property as well as the finding of suitable coating substance for each type of work.
For the method of deposition by sputtering, the coating substance will be created from the sputtering process. It is the process making atoms of coating substance to get off from surface of the target of coating substance by hitting of ions having high energy. Then it triggers the exchange of energy and momentum between the hitting ions and atoms at the surface of targeted coating substance. This process is a part of the interaction. When ions having high energy hit the surface of material, it will arise various phenomena.
1. Reflected Ions and Neutrals: The hogging ions may reflect from the surface of material. Most of them will reflect in form of neutral atoms arising from the conglomeration of electron at the surface of material.
2. Secondary Electron Emission: The hitting of high-energy ions may cause the emission of secondary electron from the surface of material if such hitting ions have enough high energy.
3. Ion Implantation: High-energy ions hitting the surface of material may implant into some part of material content. The depth of implantation will depend on the energy of hitting ions.
4. Altered Surface Layers: The hitting of high-energy ions at the surface of material may cause the new arrangement of atoms at the surface of material. In addition, it may lead to the lattice defect.
5. Sputtering process: When high-energy ions hit the surface of material, it will cause the process of continuous hitting between atoms of materials having high energy until emitting atoms from the surface of material. This process is called “Sputtering.”
It may conclude that the sputtering process is the bombarded method at the surface of material with high energy ions until atoms at the surface of material get off (We can notice from the erosion of sputtered surface of material). The phenomenon which atoms of material surface get off is called sputter or sputtering. The sputtering process was discovered fro a century by Grove. During that time, sputtering was the process causing the damage to cathode and grid in discharge lamp using in the experiment. However, such process has been widely applied at the moment.
Enter the Sputtering Process

1. Targeted Coating Substance will act as a target for high-energy ions to hit until occurring the sputtering process and the emission of atoms of coating substance.
2. High-energy ions which will hit targeted coating substance and make atoms of such target get off may be made by accelerating ions under the electric field. It can control the level of ion’s energy as demand. Although the electron will be an ion having one kind of discharge which can be easily produced and accelerated to have high energy under the electric field, the electron has less mass than atoms of coating substance considerably. Thus the transfer of energy and momentum to the coating substance is inefficient. Then the sputtering process can not occur. However, the collision of particles will have the best transfer of energy and momentum when both particles have equal mass. Therefore, it normally selects the acceleration of gas ions in the electric field to be high-energy ions for hitting the targeted coating substance.
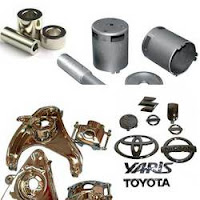
In practice, targeted coating substance is the substance bringing to coat the material or output. The high-energy ions which will make the sputtering use ions of Argon gas because it is the inert gas with suitable mass and not too high price. For the production of high-energy ions (ions of Argon gas), it will use the glow discharge process in form of plasma. Then it will be pulled or accelerated high-energy ions from plasma to hit targeted coating substance until triggering the sputtering process for creating atoms of coating substance with electric field.

From the mentioned factor, new system of DC magnetron sputtering is developed by using the magnet to help in the glow discharge process. (Using magnet may be either permanent magnet or electro-magnet). In case of DC sputtering system, it may install magnet at the back of targeted coating substance. This installed magnet will create the magnetic field in the direction which is parallel to the surface of targeted coating substance and perpendicular to electromagnetic field. Therefore, electron in the glow discharge process will have the curved movement which will help increase the distance of electron. It leads to higher ionization of inert gas resulting in higher rate of sputtering and deposition.
One method of improving surface of the material can be implemented by coating the suitable substance in from of coating layer or thin film having high quality. It can categorize into 2 large groups. transport logistics
ReplyDelete