The stainless steel is widely used in the industry because it has special features from other materials such as a good resistance of corrosion, the ability to work under high temperature, fine surface and a variety of its properties which can bring to produce numerous products such as the use of stainless steel to produce kitchenware, sanitary ware and decorations. In addition, it can bring to use for welding parts in the industrial sector such as pressure tubes, tanks, exhaust system in automobiles, equipment in the industrial factories of chemistry and food, etc.
Stainless steel has various categories. It will differ according to the chemical composition having the effect towards microstructure, the mechanical property and the application. Manufacturers should have skills, knowledge and the capability in welding each group of stainless steel . Each category will be different depending on the production process in each product. Therefore, the building of body of knowledge in manufacturers to understand the property of material which will be brought to produce is very crucial to the
industrial sector. This issue of Innovation World Magazine, “Know How” Column presents tips and techniques in welding the stainless steel and the correc6tion of production problem for creating the highest efficiency.
The important features of welding various kinds of stainless steel can be categorized as follows. 1. Austenitic Stainless Steel: This kind of steel can be easily welded. In addition, it can be welded without using heat before and after welding. The cautious thing in welding is the outcome from too high heat which will lead to the coarse grain and can not resist impact force. High temperature may cause the welding output to be distorted because this group of stainless steel is high thermal expansion but has low thermal conductivity compared to carbon steel.
The method of correction can be implemented by adjusting the electricity in welding to be low for controlling the heat input or implementing the preheat treatment for making the output to have constant temperature or preventing by using jig to hold the welding output. Furthermore, Back Step Welding and Balanced Sequence Welding or gradual welding can help reduce the distortion of output. Another problem is the arising of Chromium Carbide around the welding seam so it lacks the creation of chromium oxide film for preventing rust. The welding area will be easy to corrode. The solving of problem can be done by using stainless steel having low carbon such as 316L or the combination of Titanium or Niobium (Stabilized Grades) such as 347, etc.
2. Ferritic Stainless Steel: the welding of this category of stainless steel resembles the welding of carbon steel but it should be careful in many things such as much growing of grain from the impact of Heat Affected Zone (HAZ) or t he arising of carbide leading to the brittle welding seam. Therefore, the implementation of welding seam to have the thickness and high quality must preheat the output at 100 – 120 C before welding. In addition, the welding must control the heat input to be the least. The dissolution or improvement of carbide from welding can be implemented by heating after Post Weld-Heat Treatment (PWHT) at 750 – 850 C for 30 – 60 minutes. It will not only help reduce the residual stress within welding seam and improve the property of ductility and toughness but also lessen the resistance to the corrosion at the area affecting the heat.

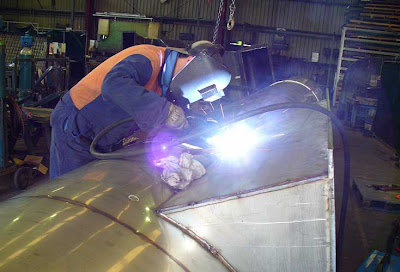
The selection of welding rod for using in the welding of ferritic stainless steel can be both ferritic and austenitic welding rod. The strength is to get the welding seam which and resist impact force increasingly. For welding outputs having the thickness more than 6 mm., it must control the heat input to be the least and use the austenitic welding rod as well.
3. Martensitic Stainless Steel: The welding of this kind of stainless will be different from the welding of austenitic and ferritic group. The structure of this kind of material is hard but brittle so it has the opportunity to be brittle when bringing to apply immediately without passing preheat and post-heat treatment. The risks of brittle will increase when the quantity of carbon increases.
For solving such problem, it can preheat at the temperature about 200 – 300 C, control the heat input and interpass temperature for helping the cooling of welding seam constantly and reduce the residual stress and the risk of cracking. Another problem which may encounter is the hydrogen embrittlement which can prevent by selecting the welding process having low hydrogen such as TIG of MIG and controlling the source of hydrogen from flux and electrode using in welding of preheat treatment. Furthermore, pos heat treatment at 650 – 750 C will help the welding seam to have good quality, improve the mechanical property, reduce the residual stress and help hydrogen which is dissolved within welding seam to spread as well.
Outputs having low quantity of carbon and thinner than 3 mm. can be welded without implementing the preheat treatment but it should use the welding process having low hydrogen. Outputs having more thickness and carbon more then 0.1% need to implement the preheat and post-heat treatment for reducing the stress and helping spread hydrogen from the welding seam.
After welding the stainless steel, it will enter the cleaning process of welding seam. The process will be: 1. To eliminate scale and clean up the surface of welding seam by using chemical. Mostly, it will use HNO3+HF acid solution in eliminating various defects from welding such as scale or burning-mark. It should not use with austenitic stainless steel occurring Sensitization (Losing of Chromium in form of carbide) or the area of parts touching with carbon steel. In addition, it also applies gel at t he welding seam for eliminating scale and cleaning up. The benefit of using gel is to help clean up welding seam at the vertical line. It can also clean up through the mechanical process such as the surface grinding with Grinding Wheel or polishing with Power Brushing or Sand Blasting by polishing with stainless steel wire brush, etc. This will help eliminate metal scrap from welding on the surface of metal plate or welding seam or slag from flux covering welding rod. However, the disadvantage of this process is that it is difficult to notice small defects.
2. The implementation of Passivation by using concentrated nitric acid of 20 – 40% at the temperature at 50 – 60 C for creating the forming of chromium oxide film and washing after the implementation of Passivation.
This presentation of welding techniques in various kinds of stainless steel and cleaning will benefit readers who can bring this body of knowledge to develop their own production process and business for having the competitiveness with sustainability.
No comments:
Post a Comment